Then the real work started.
This guy removed the spikes from the old ties.

(Click on images to enlarge)
He did that by lining up a little notched plate on the arm of his machine with each spike. Precision work and patience!
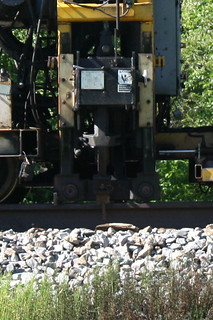
They were working on the north track only. The south track was for trains. Work had to stop while this train passed through, since (I'm guessing) the tie crane didn't have room to rotate.

Step 2 was the tie exchanger, pulling the old ties out from under the rails. Most of the ties came out all in one piece, but the more rotted ones fell apart, and the exchanger had to spend some time getting all the fragments out.

The front mechanism raised the rails off the ties to make it easier to pull them out.

This machine makes it look so easy! Think of the manpower this work required, before the invention of the tie exchanger.
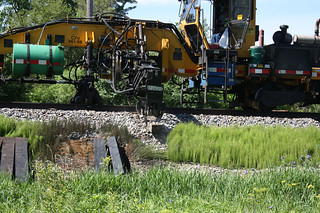
Speaking of manpower — these guys had to walk the line behind the tie exchanger, retrieving the anchor plates from the old ties. Those plates would be re-used on the new ties.
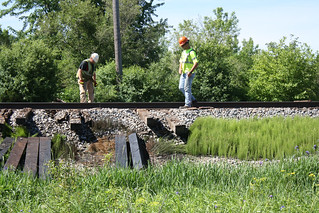
Then another tie crane picked up the old ties and stacked them at intervals along the way.

Now, I don't know what this machine is, or exactly what it was doing — it appeared to be clearing ballast away from each tie position.

Tie Crane No. 3 just moved each new tie into position to be slid under the rails …

… and the sliding-under-the-rails part was done by Tie Exchanger No. 2.

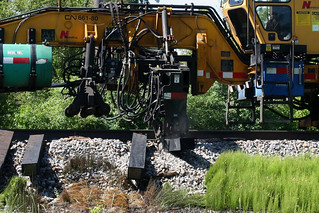
A small sweeper followed, clearing away ballast, fragments of tie wood, and any other debris from atop the new ties.

Walking behind the sweeper, several men picked up anchor plates the old-fashioned way, with low-tech metal tools, and put them atop the new ties, ready to be slid under the rails. That job was done by the guy at right in the picture below. His metal tool was anything but low-tech, being electronically connected to that little machine; he'd push a button, the machine would raise the rail, he'd slide the anchor plate into position under it, then instruct the machine to let down the rail. And so on for each tie.
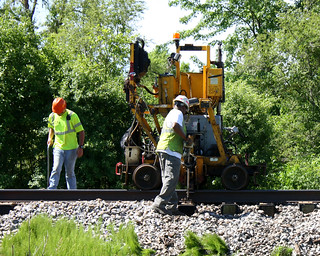
Next came our old pal, the ballast tamper, firming up the ballast under each new tie.

Bringing up the end of the parade was the spike-driving machine, pounding the spikes through the anchor plates to hold the rails to the new ties.

It sounded like a machine gun firing short bursts. You couldn't really see the hammering action, as that part of the mechanism was shielded by a heavy metal screen.

One crew member sat in the cab hand-loading spikes into the feed tube.
And that was how they put in the new ties. I watched them all morning, and by the time they got through I was as tired of railroad maintenance as you people are. But I just had to post this. The railroad probably won't need new ties again for 10 years, by which time I don't expect to be blogging!
No comments:
Post a Comment